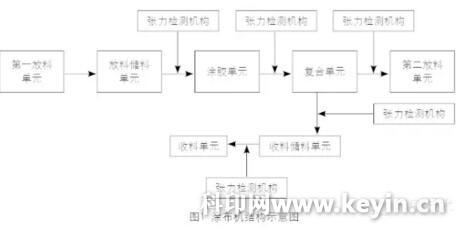
The above content is reproduced in the " Printing Technology " official WeChat (Printech1957) , authorized by the company to publish, copyright, piracy will be investigated !
Galvanized Hexagonal Wire Netting
ŸGalvanized hexagonal wire mesh is also named Chicken wire netting, made of low carbon iron wire, galvanized or hot-dip zinc plated before or after weaving. Hexagonal Wire Netting is firm in structure and has flat surface. It is extensively used in INDUSTRIAL AND AGRICULTURAL CONSTRUCTUONS AS REINFORCEMNET AND FENCING. It is also used as Fence for Poultry Cage, Fishing, Garden and Children playground, etc.
Assortments Available for galvanized hexagonal wire according to processing:
Hexagonal wire, Electro Galvanized before Weaving
Hexagonal wire, Electro Galvanized After Weaving
Hexagonal wire, Hot Dipped Galvanized before Weaving
Hexagonal wire, Hot Dipped Galvanized after Weaving
Galvanized chicken wire netting |
|||||
Mesh |
Min. Gal.v. G/SQ.M |
Width |
Wire Gauge (Diameter) BWG |
||
Inch |
mm |
Tolerance (mm) |
|
|
|
3/8" |
10mm |
±1.0 |
0.7mm - 145 |
0.5m - 1.0m |
27, 26, 25, 24, 23 |
1/2" |
13mm |
±1.5 |
0.7mm - 95 |
0.5m - 2.0m |
25, 24, 23, 22, 21 |
5/8" |
16mm |
±2.0 |
0.7mm - 70 |
0.5m - 2.0m |
27, 26, 25, 24, 23, 22 |
3/4" |
20mm |
±3.0 |
0.7mm - 55 |
0.5m - 2.0m |
25, 24, 23, 22, 21, 20, 19 |
1" |
25mm |
±3.0 |
0.9mm - 55 |
0.5m - 2.0m |
25, 24, 23, 22, 21, 20, 19, 18 |
1-1/4" |
31mm |
±4.0 |
0.9mm - 40 |
0.5m - 2.0m |
23, 22, 21, 20, 19, 18 |
1-1/2" |
40mm |
±5.0 |
1.0mm - 45 |
0.5m - 2.0m |
23, 22, 21, 20, 19, 18 |
2" |
50mm |
±6.0 |
1.2mm - 40 |
0.5m - 2.0m |
23, 22, 21, 20, 19, 18 |
2-1/2" |
65mm |
±7.0 |
1.0mm - 30 |
0.5m - 2.0m |
21, 20, 19, 18 |
3" |
75mm |
±8.0 |
1.4mm - 30 |
0.5m - 2.0m |
20, 19, 18, 17 |
4" |
100mm |
±8.0 |
1.6mm - 30 |
0.5m - 2.0m |
19, 18, 17, 16 |
Note: |
- ŸMesh from 25 mm are reverse-twisted,
-
Mesh smaller than 25 mm are twisted three
times.
For strengthening wire mesh purposes:
-
This wire mesh could has double edged Wires and the height
-
From
100 cm at the mesh from 25 mm are provided with an extra horizontal wire for
better stability.
- Mesh smaller than 25mm could also be made twisted five times, ensures that the product has higher resistance.
Galvanized Hexagonal Wire Netting,Galvanized Chicken Wire, Hot Dipped Galvanized Hexagonal Wire Mesh,Stainless Steel Bird Wire Mesh
DINGZHOU TIAN YILONG METAL PRODUCTS CO., LTD. , https://www.wiremeshsolution.com